Meira Oy on suomalainen kahvi- ja mausteteollisuuteen erikoistunut yritys. Sen juuret ulottuvat vuoteen 1914 Helsingin Erottajalle, jolloin kahvipaahtimo aloitti toimintansa. Maustetehdas avattiin vuotta myöhemmin. Kahvipaahtimo ja maustetehdas siirtyivät Aleksis Kiven kadulle 1930-luvulla, jossa ne toimivat edelleen.
Saimme aamuisen yhteydenoton Vallilan tehtaalta, kun kahvinpakkauskoneen pakkauskuljettimen vaste (puhutaan lempinimellä käpälä) oli vaarassa loppua varastosta kokonaan. Vaste toimii myös sulakeosana, jonka tarkoitus on murtua rikki ja pysäyttää kone, kun linjastolla sattuu kolari ja suojella linjastoa näin suuremmalta vahingolta. Osan uusimistarve vaihtelee koneen mekaanisesti vikaantuessa tai pakkauksen virheellisen muodon mukaan. Sillä hetkellä varastossa olevat osat eivät riittäisi välttämättä edes tulevan viikonlopun yli, joten tarve oli kova ja akuutti. Laitevalmistaja oli ilmoittanut tarjoamansa varaosan toimitusajaksi vähintään kaksi kuukautta.
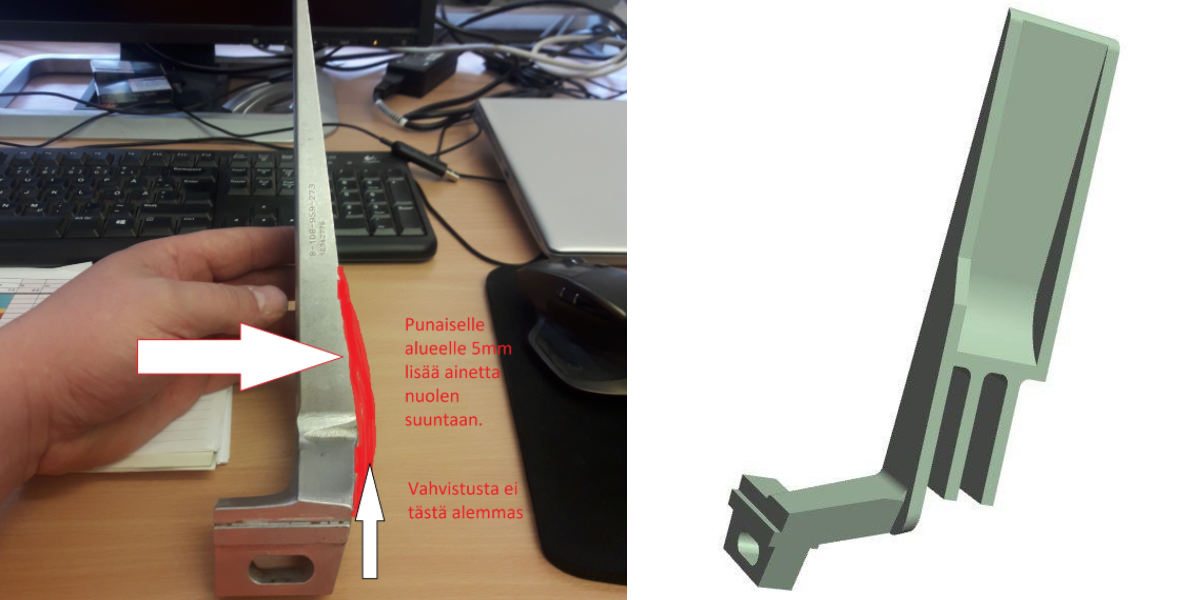
Käpälän muokkausohjeita ja digitaalinen malli.
Etenimme Meiran kanssa nopeasti ensimmäisen yhteydenoton jälkeen. Sovimme tapaamisen heti samalle aamupäivälle. Saimme sieltä mukaamme viimeisimpinä olevan ehjän alumiinivalmisteisen varaosan. Muutimme toimistollamme osan geometrian digitaaliseen 3D-muotoon mallintamalla ja palautimme alkuperäisen osan vielä samana päivänä Meiralle. Muodoiltaan käpälän 3D-skannauskin olisi ollut meillä mahdollista, mutta mallintamalla osa uudestaan yksittäisten mittojen muuttaminen helpottuu.
FDM-tekniikalla yön yli valmistetusta protosta asiakas pystyi kommentoimaan mallia ja valitsemaan mieleisen materiaalin sampleista heti seuraavana päivänä. Teimme vielä muutaman pyydetyn korjauksen malliin, jonka jälkeen valmistimme sarjan osia lasersintraamalla tulevan kahden viikon kriittisimpään tarpeeseen. Elintarvikeolosuhteisiin hyväksytty polyamidi (Duraform ProX PA12) valikoitui materiaaliksi. Sarja toimitettiin asiakkaalle neljän päivän sisällä ensimmäisestä yhteydenotosta. Tämän jälkeen osaan on tullut vielä pieniä muutoksia käytöstä tulleiden kokemusten perusteella. Suurimmat hyödyt asiakkaan mukaan ovat olleet toimitusnopeus ja hinta verrattuna alkuperäisosaan.
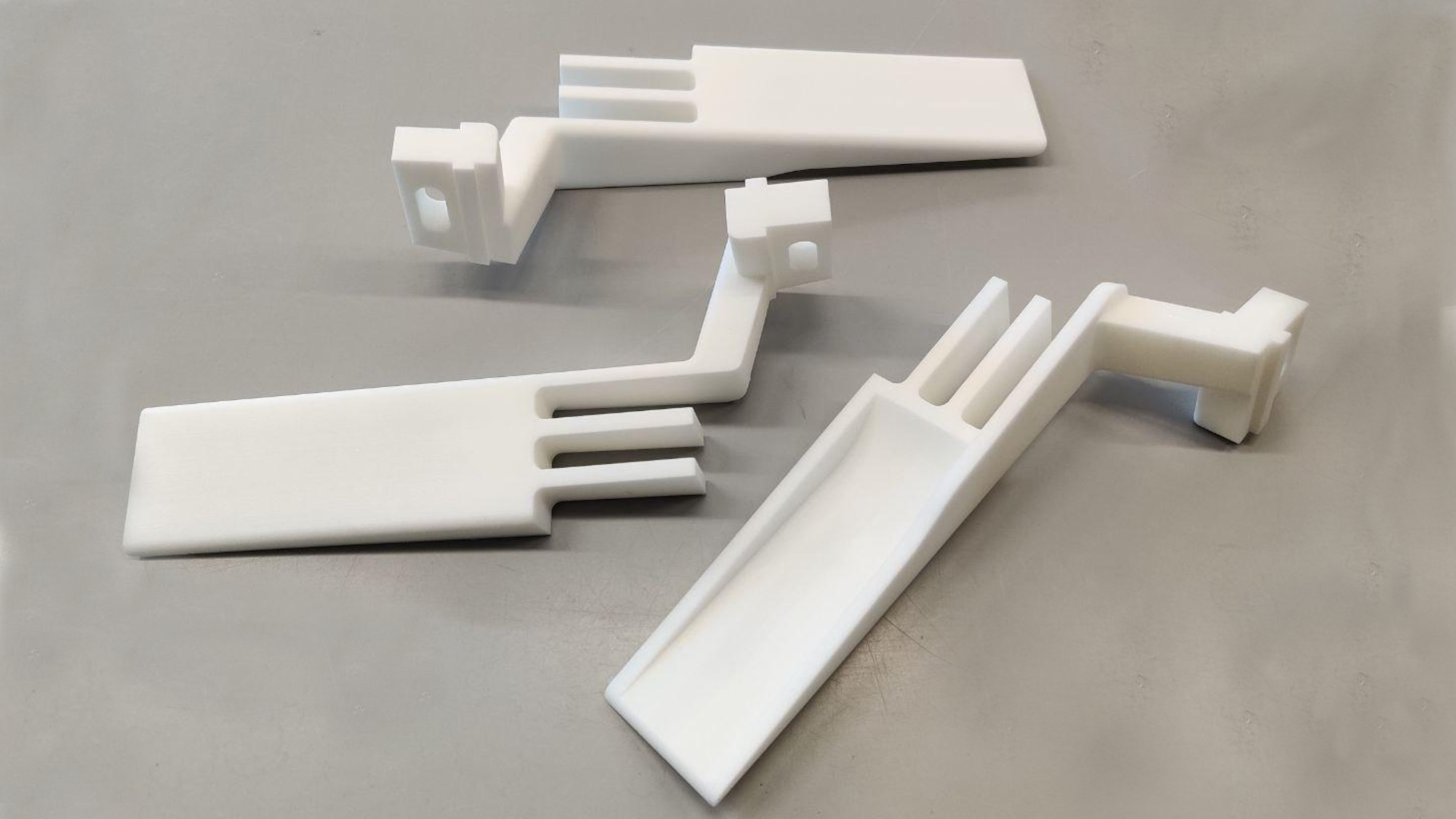
Duraform ProX -materiaalista valmistettuja käpäliä.
20-luvun varaosat
3D-tulostetut digitaaliset varaosat ovat yksi nopeimmin kasvavista trendeistä 3D-tulostuksen alalla. Kasvava kysyntä liittyy tuotteiden valmistuksen uusiin mahdollisuuksiin siirtyä entistä enemmän paikalliseen älykkääseen tuotantoon. Osien valmistus tehdään tarpeen mukaan 3D-tulostamalla ja yleensä lähellä käyttökohdetta. Näin pystytään heti vähentämään logistiikkakuluja. “Tämä luo useita houkuttelevia etuja perinteiseen toimintamalliin nähden, jossa osat voivat olla pitkien toimitusketjujen takana vaikeasti saatavilla”, kertoo Tohtori Mika Salmi Aalto Yliopistolta digitaalisia varaosia koskevassa tutkimushankkeessa.
Tänä päivänä yhä useammat yritykset ovat ottamassa ensiaskeleensa varaosien digitoinnissa. Mahdollisuus tulee usein ensimmäistä kertaa esille suorasta tarpeesta, kun tietty osa on loppumassa ja sitä tarvittaisiin käyttöön nopeasti ja huomataan, että varaosaa ei löydy tai sitä ei enää valmisteta. Toimitusmäärät saattavat myös olla rajattu isoihin kappalemääriin, jolloin vain muutaman kappaleen tarpeeseen pitäisi tilata turhan suuri erä. Joskus pelkkä varaosien pitkä toimitusaika ja korkea hinta saavat jo miettimään muita vaihtoehtoja.
Erilaiset tuotantovaihtoehdot avautuvat selkeämmin kun osa on digitoitu. Samalla kun alkuperäinen malli digitoidaan, se voidaan myös suunnitella uudelleen sopimaan paremmin käyttötarkoitukseensa. Joissain tapauksissa geometriaa optimoimalla voidaan valmistaa kevyempi ja vahvempi osa. Joskus pelkkä tuotantotekniikan ja materiaalin vaihto tuo selviä etuja. Perinteiset valmistusmenelmät eivät tule katoamaan, eikä materiaalia lisäävä valmistus kuten 3D-tulostus, tuo ratkaisua kaikkiin ongelmiin. Osien digitointi tuo kuitenkin lisää uusia valmistusmahdollisuuksia ja vaikuttaaa näin samalla varaosien saatavuuteen.
Business Finlandin, VTT:n ja Aalto Yliopiston digitaalisten varaosien mahdollisuuksia tutkiva DIVA-hanke arvioi, että jo tällä vuosikymmenellä merkittävä osuus varaosista tullaan valmistamaan 3D-tulostamalla.
Terveisin,
Svante Knuus
Tuotepäällikkö – Maker3D